
Multidisciplinary Advanced Engineering Consultants and Software Developers
Pioneers in Engineering Automation and Digitisation
Flow Assurance
Vessel Calcs
Structural Analysis
Finite Element Analysis
At Advanced Analysis, we specialize in conducting analytical vessel fire risk studies for various types of pressure vessels.
Our team of experts is proficient in taking a detailed approach to this type of analysis by performing coupled Finite Element Analysis (FEA) and Computational Fluid Dynamics (CFD) analysis. This includes modelling jet fires impinging on the vessel and using FEA to calculate the heat-up of the vessel.
Radiant heat loads resulting from impinging jet fires on targets of concern are evaluated to determine the requirements for Passive Fire Protection (PFP).
​
We consider various factors such as blowdown (duration or pressure threshold) and cladding vessel liquid evaporating contents in these types of calculations to provide a more comprehensive analysis.
Advanced software packages, such as ANSYS, ABAQUS, NASTRAN, and others, are utilized to ensure accuracy and reliability in our analyses.
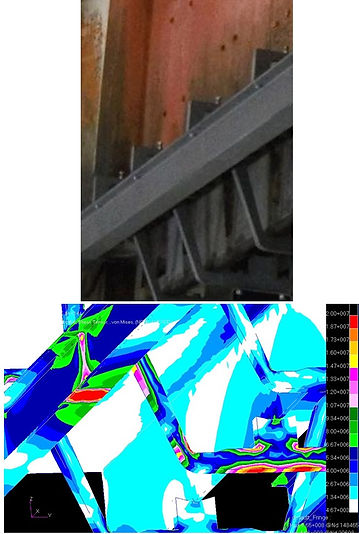
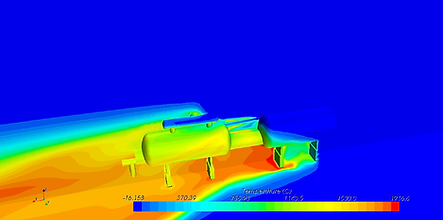

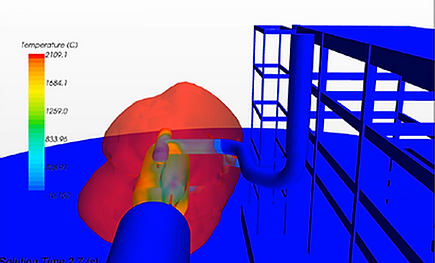
Flow Assurance
PIPESIM OLGA HYSYS CFD
Our company specializes in solving complex flow problems related to venting, flaring, and depressurization calculations, which are critical to determine the lowest temperature at which steel/alloy fittings, piping, and vessels reach to prevent embrittlement that can lead to catastrophic failures. Our expertise also covers the formation of liquid droplets in gas pipeflows that can cause significant damage at pipe bends or junctions, as well as the induced vibrations from high-speed flows.
​
In addressing these challenges, we use various software packages such as PIPESIM, HYSYS, and OLGA. Computational Fluid Dynamics (CFD) is employed for more complex problems that involve 3D fluid effects, turbulence, and multiple flow phases (liquid, gas, and foam).
​
Our team of experts has provided solutions to various companies globally, including BP, Shell, Woodside, ADNOC Sour Gas, ADNOC Gas Processing, ADNOC Onshore, ADNOC offshore, Carigali, Hess, WorleyParsons, FLUOR, Technip, Genesis, and many others.
Flow Assurance Methodology
OLGA Study
The methodology for an OLGA study is relatively straight forward. A model of the pipeline system including inlets and outlets and other features such as restrictions/orifices are created.
Model information should include the pipeline lengths and elevations, as well as other physical dimensions such as diameter and roughness.
Information for pipeline materials including the pipe material itself (e.g. steel or aluminium), as well as, insulation (if applicable) should also be included in the model. This can automatically specify heat transfer coefficients (specific heats, etc.), as well as pipe roughness which is important for turbulence quantification.
Mass flow rates, fluid properties (such as density, specific heats and others) are added to the model and initial conditions including initial pressures temperatures, composition and quality are also specified.
Flow scenarios are then modelled to obtain relevant pressures and temperatures. Typical scenarios involve checking pressures and temperatures, as well as examining the low-temperature effects of high-speed gas flows (such as venting, depressurization, or flaring), which can cause embrittlement. These outcomes are verified through the OLGA study. Slugging is also a typical feature of the flow that is commonly investigated. This results in high internal forces on pipelines particularly at bends or high gradient elevation changes.
Recommendations are made with reference to material selection for piping, as well as flow parameters or design features which can prevent or mitigate the risk of elevated pressures or temperatures in the pipeline system under investigation.
Surge Study
A model of the crude or water pipe system, including pipe lengths, diameters, restrictions, and connections such as valves and pumps, is created in pipeline software such as TLNET, Pipeline Studio-Liquid, or Bentley Hammer.
Important features of the model include the pipeline profile (especially the elevations and location of high points), pipeline and lining material, inventory locations, connections, and roughness. Pump characteristics such as performance curves, operating speeds, and moments of inertia are also included.
​
Scenarios where surge is a risk are then investigated using the model. Surge is a sudden increase in pressure or flow rate in the pipeline, which can damage the pipeline or equipment. Surge can occur due to pump start-up or shut down, loss of power, valve shutdown, air pocket or vacuum creation, or rapid removal. Surge associated with these cases can be identified, and recommendations can be made for prevention and mitigation, such as flow rate control or surge control methods like surge tanks or pressure relief valves.
PIPESIM Overview
PIPESIM is a flow simulation software program that is used for modeling both steady-state and transient multiphase flows. Mid-sized and large companies in both the oil and gas industry use PIPESIM to understand the behavior of fluids in their systems under various operating conditions. As part of normal use, PIPESIM can optimize production, diagnose operational challenges, and simulate pipeline design scenarios using its computational fluid dynamics (CFD) capabilities. More information about PIPESIM can be found at https://www3.technologyevaluation.com.